Battery testing serves to inform us about key aspects of individual cells and battery groups that we wish to understand.
Common questions include:
Is the battery fully charged?
How much charge remains in the battery?
Does it meet the manufacturer’s specifications?
Has there been any decline in performance since its new state?
What is its expected longevity?
Do all safety devices function properly?
Does it produce interference or electrical noise?
Is it susceptible to interference or electrical noise?
The answers to these questions are not always clear-cut.
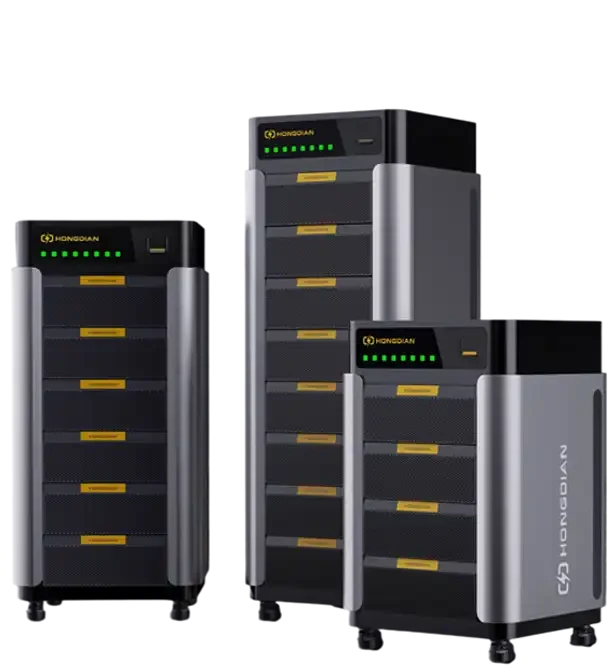
Indirect Measurements
While all cell parameters that a design engineer might want to measure can be quantified through direct measurement, this is not always convenient or feasible. For instance, the state of charge (SOC) of a battery can be determined by fully discharging it and measuring the energy output. However, this method is time-consuming, wastes energy, shortens battery life with each test cycle, and may not be practical if the battery is in use. It is also ineffective for primary cells. For more detailed information on how this is done, see the State of Charge page.
Similarly, the remaining life of a secondary cell can be determined by continuously cycling it until failure, but this knowledge is irrelevant if the cell must be destroyed in the process. This is known as the state of health (SOH) of the battery.
What is needed are simple tests or measurements that can serve as approximations or indirect measures of the desired parameters. For more information, see the State of Health page.
Cell Design Process Testing
A much more rigorous testing regime is necessary during the design of new cells. More information can be found on the New Battery Designs and Chemistries page.
Test Conditions
For all tests outlined below, and testing in general, the test conditions must be specified to ensure repeatable results and meaningful comparisons. This includes factors such as method, temperature, depth of discharge (DOD), load, and duty cycle. For instance, cell capacity and cycle life, two key performance indicators, could vary by 50% or more depending on the temperature and discharge rate during testing. See also Cell Performance Characteristics.
Battery specifications should always include test conditions to avoid ambiguity.
Qualification Testing
Qualification testing is designed to ascertain whether a cell or battery is suitable for its intended purpose before being approved for use in a product. This is particularly crucial for cells used in “mission critical” applications. These comprehensive tests are initially conducted on a limited number of cells, including testing some to destruction if necessary. As a subsequent stage, qualification testing also involves examining completed battery packs before the product is approved for customer release. The tests are typically performed to confirm that the cells meet the manufacturer’s specifications but can also be used to test the cells against arbitrary limits set by applications engineers to determine how the cells perform under adverse conditions or unusual loads, to identify failure modes, or to assess safety factors.
The battery packs should also be tested with the charger recommended for the application to ensure compatibility, particularly evaluating potential user patterns to prevent overcharging. See also the section on Chargers.
Mechanical Testing
Typical tests are included in the safety standards below and range from simple dimensional accuracy checks to dynamic testing to ensure the product can withstand any mechanical stresses it may encounter.
Environmental Testing
Typical tests are included in the safety standards below and are designed to subject the product to all the environmental conditions it is likely to experience during its lifetime.
Abuse Testing
The goal of abuse testing is to confirm that the battery poses no danger to the user or itself in the event of accidental or deliberate mistreatment under any conceivable conditions of use. Designing fail-safe batteries is increasingly challenging because, as we know, misuse can be incredibly creative.
Abuse testing (always fascinating to observe) is typically specified as part of the Safety Testing (below). Recent incidents involving lithium cells have highlighted the potential hazards, leading to stricter battery design guidelines, a broader range of tests, and more stringent transport regulations for shipping the products.
Safety Standards
Consumer products usually must comply with national or international safety standards required by the safety organizations of the countries where the products are sold. Examples include UL, ANSI, CSA, and IEC standards.